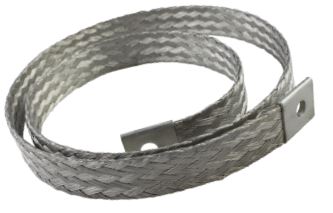
Bonding jumpers are critical components in electrical systems, ensuring safety, reliability, and compliance with electrical codes. These flexible conductors are used to establish electrical continuity between metal parts or between a grounding system and electrical components. By creating a low-resistance path, bonding jumpers prevent electrical shocks, equipment damage, and fire hazards.
What is a Bonding Jumper?
A bonding jumper is a conductor or strap designed to connect two parts of an electrical system, ensuring they share the same electrical potential. This connection prevents dangerous voltage differences that can lead to equipment malfunction or safety hazards. Bonding jumpers are typically made from highly conductive materials such as copper, aluminum, or tinned copper, and are often insulated or bare, depending on the application.
Industrial Applications of Bonding Jumpers
Bonding jumpers are widely used in various industries to enhance safety and functionality in electrical systems:
- Construction: Ensures proper grounding in residential, commercial, and industrial buildings, protecting occupants and equipment.
- Telecommunications: Provides grounding and bonding for antennas, communication towers, and equipment racks.
- Renewable Energy: Used in solar power systems to bond solar panels and inverters to the grounding system, ensuring safety and compliance.
- Transportation: Ensures electrical continuity in vehicles, railways, and ships to prevent stray currents and maintain system reliability.
- Petrochemical and Gas: Bonds equipment in hazardous environments, reducing the risk of static discharge and explosion.
Properties of Bonding Jumpers and Their Functions
1. Material Conductivity
Copper and tinned copper are the most common materials used due to their excellent electrical conductivity and resistance to corrosion. Aluminum is also used for its lightweight properties and cost-effectiveness in certain applications.
2. Flexibility
Bonding jumpers are designed to be flexible, allowing them to connect components even in tight or irregular spaces. This flexibility also reduces stress on connections, ensuring durability.
3. Insulation
Insulated bonding jumpers are used in applications where contact with other conductive parts must be avoided, preventing short circuits.
4. Size and Gauge
Bonding jumpers are available in various sizes and gauges to match the specific current-carrying capacity and mechanical requirements of the application.
5. Weather Resistance
For outdoor or harsh environments, bonding jumpers are often coated or made from materials resistant to moisture, UV rays, and temperature extremes.
Advantages of Using Bonding Jumpers
- Improved Safety: Bonding jumpers reduce the risk of electrical shocks and fires by maintaining electrical continuity.
- Enhanced System Performance: By minimizing voltage differences, bonding jumpers ensure consistent operation of electrical systems.
- Regulatory Compliance: Meeting electrical codes and standards, bonding jumpers contribute to system reliability and legal compliance.
Conclusion
Bonding jumpers are essential components in electrical systems, offering safety, efficiency, and reliability across numerous industries. Their ability to maintain electrical continuity, prevent hazards, and ensure compliance makes them indispensable in applications ranging from construction to renewable energy. With a variety of materials, sizes, and configurations available, bonding jumpers can be tailored to meet specific requirements, ensuring optimal performance in any environment. Investing in high-quality bonding jumpers is a crucial step in building safe and efficient electrical systems.